Off-shore Structural Health Monitoring
Continuous contact between marine structures and hostile environment. Therefore, it is essential to monitor the structure's condition to prevent catastrophic events. For instance, data indicates that mooring line failures occur on average every 9 years, despite the fact that mooring lines are designed to last 25 years. Acoustic Emission characterization is one of the techniques that can be used to detect deterioration in mooring cables, such as cracks and load based strain.
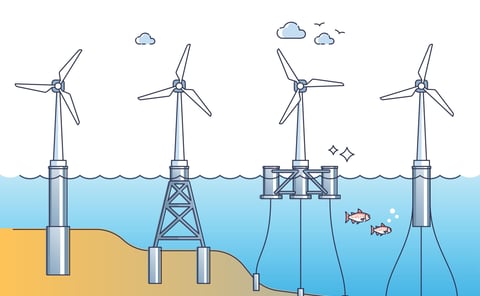
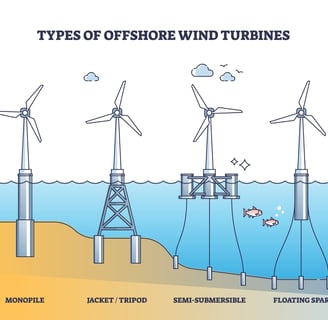
BEV Charging/FCEV/T Refueling Systems
· Charging System health including interfacing to corresponding vehicle computer to fingerprint the vehicle before charging or fueling begins.
· Insurance claim reduction
· Notification to driver/OEM and cloud based data capture for Dealer maintenance record/file history from both the vehicle and any system historically interfaced to it
· Power Quality assessment of the charging system and notification for maintenance – increased uptime, pro-active maintenance
· Reduced cost of ownership and increased customer satisfaction.
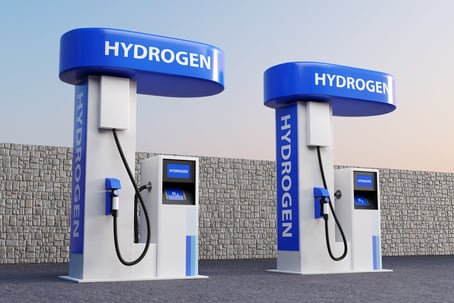
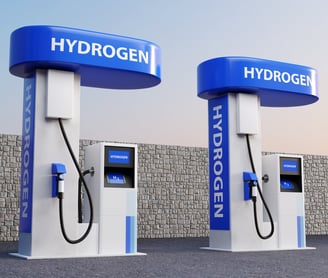
Monitoring a hydrogen-handling reciprocating compressor is essential for its safe and efficient operation. Consider the following factors when monitoring a hydrogen reciprocating compressor:
Pressure Monitoring: Regularly measure the compressor's suction and discharge pressures. Observe for any irregular fluctuations or deviations from the normal operating range. Sudden pressure drops or surges may indicate problems such as leaks, faulty valves, or an overloaded compressor.
Observe the temperature at various locations throughout the compressor, including the suction and discharge temperatures. Temperatures that are too high may indicate problems such as insufficient cooling, bearing issues, or ineffective compression. Continuous monitoring facilitates the detection of anomalies and the prevention of potential equipment malfunctions or safety hazards.
Utilize vibration monitoring techniques to determine the condition of the compressor. Excessive vibrations may indicate misalignment, deteriorated bearings, unbalanced rotating components, or other mechanical problems. Regular vibration analysis can aid in identifying and resolving issues before they worsen and cause extensive damage.
Hydrogen is a highly flammable gas, so it is essential to monitor the compressor system for leakage. Install gas leak detectors or use other methods, such as hydrogen sensors, to quickly detect any gas leakage. Early leak detection prevents safety hazards and guarantees the system's integrity.
Lubrication Monitoring: If the reciprocating compressor requires lubrication, the purity and levels of the lubricant should be monitored frequently. Monitor the lubricant for contaminants, oxidation, or degradation, which can negatively impact the performance and lifespan of the compressor. Proper lubrication is necessary for minimizing friction, reducing corrosion, and preserving operation efficiency.
Power Consumption: Monitor the compressor motor's power consumption. Variations in power consumption that are statistically significant may indicate mechanical issues, such as increased friction, faulty valves, or piston ring wear. Unusual patterns of power consumption must be investigated immediately to prevent potential malfunctions.
Maintenance and Inspection: Establish a regular schedule for the compressor's maintenance and inspection. Critical components, such as valves, pistons, gaskets, and seals, should be routinely inspected per the manufacturer's instructions. As directed, promptly address any signs of wear or damage and perform maintenance duties such as lubrication changes, filter replacements, and valve adjustments.
Utilize a comprehensive system for data recording and analysis to record and analyze the monitored parameters. This assists in identifying trends, detecting anomalies, and establishing a normal operation baseline. The analysis of data can shed light on performance optimization, predictive maintenance, and problem solving.
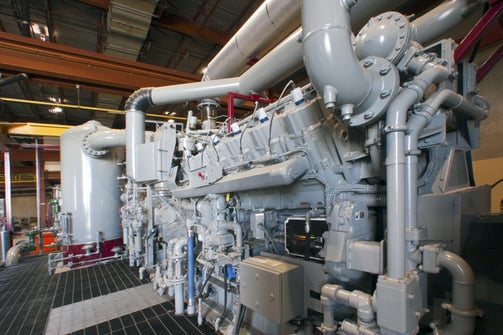
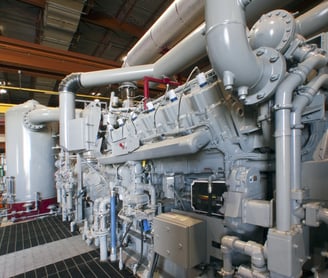